— Насколько трудным для производства оказался этот год? Смогли ли вы справиться с возникшими вызовами и той неопределенностью на рынке, которая царит до сих пор?
— Как ни парадоксально, но что касается неопределенности, наше предприятие сегодня находится, возможно, в лучшей своей форме. Последние полтора года мы работали над системой управления заказами. В начале года эта система была внедрена и сейчас показывает отличные результаты.
С неопределенностью внутри предприятия мы практически разобрались. Представьте: у вас одновременно в производстве находится сотня заказов, на каждый из которых нужно сделать по тысяче мелких и крупных деталей. Все они собираются на складе и очень друг на друга похожи, а в некоторых случаях еще и заменяемы. Какому-то клиенту невтерпеж, а кто-то не торопит нас со сроками. Возникает соблазн решить проблему за счет более терпеливого. Все смешивается, возникает путаница. Это сильно тормозит производство.
Вручную вы сможете навести порядок с десятью или даже с сотней потоков, но если таких потоков одновременно тысяча? Без автоматизации процесса управления заказами эту проблему просто невозможно решить. На базе программного комплекса 1С мы дописали своими силами эту, достаточно сложную часть, и в результате получили полный позиционный контроль прохождения отдельной детали — от заготовки до поступления готового изделия на склад. Программа оповещает о готовности всего заказа, показывает его прохождение от процесса размещения до отгрузки заказчику. По ней можно проследить движение всех комплектующих. Заранее устанавливать точное время старта и время готовности заказа на производстве. Иными словами, мы стали видеть все, что происходит в цехах и на складе в реальном масштабе времени.
— Полагаю, что результат — это только вершина айсберга.
— Вы правы. Для того, чтобы внедрить автоматический учет пришлось перенастроить все бизнес-процессы, научиться работе позаказно. Перед тем, как приступить к выполнению конкретного заказа, в программе происходит проверка, какие комплектующие и в каком количестве уже есть в запасе. Определяем наличие сырья для производства, чтобы не покупать лишнего. Запас на самом деле сильно тянет карман. Его сильно оптимизировали. Отработали блок резервирования сырья и готовой продукции.
Служба планирования определяет эффективное распределение мощностей по станочному парку, оптимальное время старта и финиша работ для равномерной загрузки оборудования. Все это перетекает в сменные задания по подразделениям и участкам на каждый день.
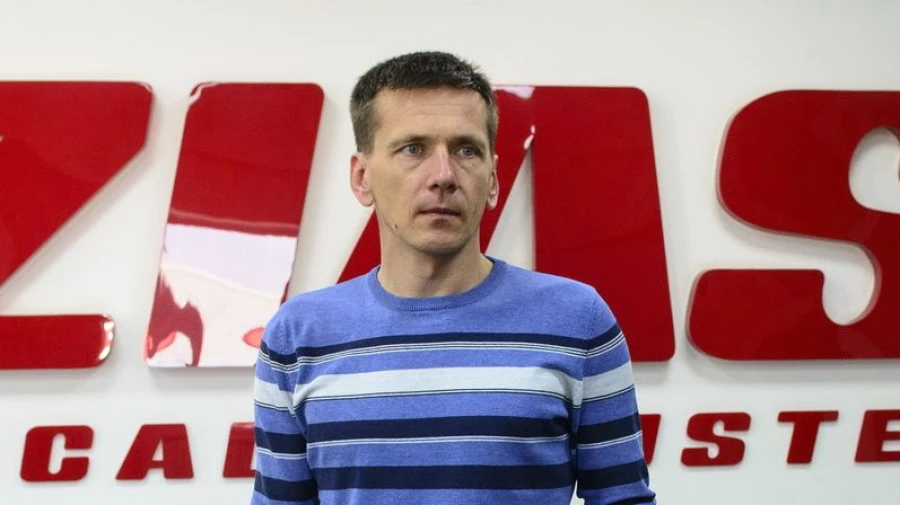
— Но как учитывать все заготовки и прохождение ими каждого передела?
— Для этого использовали штрих-кодирование. Заготовка от операции к операции меняет свой статус, чтобы «не потеряться» в процессе обработки. Программа выявляет, какие детали «зависли» и не перешли на следующий этап. В конце все комплектующие встречаются на складе, попадают в резерв по своим заказам, и бот оповещает сотрудников, имеющих отношение к отгрузке, что заказ готов. Почему бот? Да потому, что это сокращает личные коммуникации и ручной контроль. Так нам удалось победить извечный заводской хаос, имеющий место на предприятиях с огромной номенклатурой деталей.
— Многие производственники шутят, что автоматизация обычно производится для благих целей, но эффект от нее съедают понесенные на внедрение затраты.
— В нашем случае есть очень конкретный эффект. Многие предприятия работают над повышением эффективности, используя принципы бережливого производства. Все мы прекрасно знаем основные виды потерь, для всех ясно, что целью является устранение таковых, и все же остается вопрос, как конкретно их устранять, какими инструментами для этого располагает предприятие? Особенно, если каждый следующий день сильно отличается от предыдущего. Очевидно не делать лишнего, не позволять продукции подолгу ожидать своей очереди, сокращать необоснованное перемещение товара. А как это реализовать? Быстрее бегать?
Благодаря полноценной системе контроля и учета движения всех заказов, с выдачей ежедневного сменного задания, с планированием загрузки станков, у нас резко сократилось время ожидания готовых заказов, сократилась оборачиваемость, выросла производительность труда. Раньше в учете использовалось бесконечное множество эксельных таблиц, которые заполнялись вручную, шла бесконечная синхронизация информации. Производили лишнее и больше. На всякий случай. Расти в таких условиях с учетом «на коленке» сложно. Нас лихорадило несколько последних лет. Теперь мы имеем вроде бы непроизводственный актив, но с ним смело можно двигаться дальше.
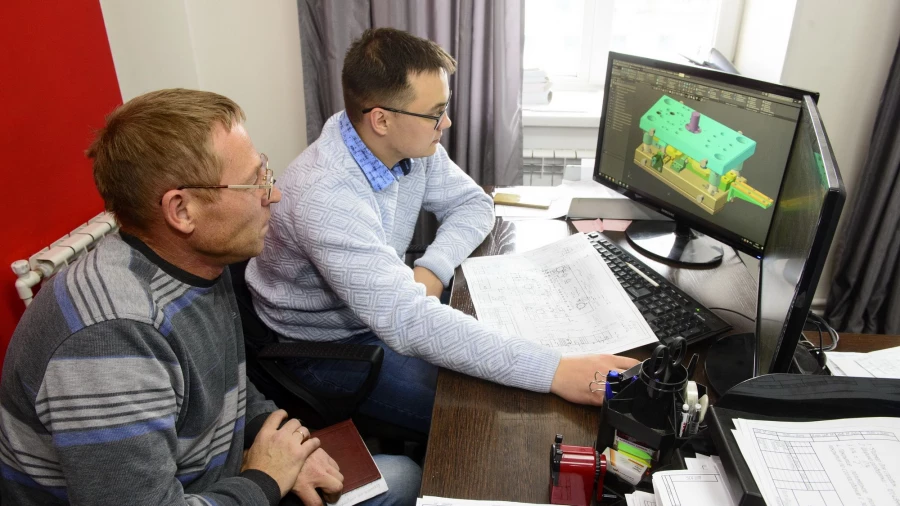
— Последует продолжение?
— Сейчас мы внедряем похожую систему в инструментальном производстве. Здесь много работ отдается на аутсорсинг. Встает вопрос, как совместить нашу внутреннюю систему с внешним миром. И здесь также поможет штрих-кодирование.
— То, о чем вы рассказали, — лишь часть большого процесса автоматизации управления. Помню, как был озадачен вашими «мультикассами» в цехах, где мастер мог распечатать сменное задание.
— Да, мы начинали с терминалов сбора и выдачи данных. Они, действительно, были сделаны нашими инженерами на базе мультикасс. Каждый вечер в систему выгружаются сменные задания, а утром каждый участок распечатывает его в терминале. Когда-то это будет делаться через смартфон или планшет. Нашей системой заинтересовались коллеги. Многие алтайские предприятия хотели взять ее на вооружение, в том числе, вам известные — «Мартика», «Тонар», «СиСорт», «Алмаз».
Следующие на очереди по автоматизации системы управления заказами — конструкторская и технологическая службы. Заказы и контроль над их выполнением должны для этих служб ставиться через CRM. Над этим нужно еще поработать.
— А как обстоят дела с загрузкой предприятия?
— Можем делать и больше, и в то же время наблюдаем явное оживление рынка, как по основному продукту, так и по инструментальному направлению. И это оживление на рынке придает уверенности. В инструментальном производстве, помимо заказов на штучное изготовление вышедших из строя деталей, к нам стали обращаться с интересными в коммерческом отношении задачами. Помочь коллегам из Бочкарей, тому же «СиСорту», или Поспелихинской макаронной фабрике — не вопрос. Но это — разовая работа по себестоимости. А вот изготовление комплектующих для предприятия-поставщика коммуникационного оборудования «Россетей», или расходников для транспортеров — уже бизнес.
Нашей команде интересно постоянно создавать, конструировать что-то новое, решать сложные инженерные задачи. Это, если хотите, в крови нашего коллектива. Сейчас мы инициативно разрабатываем уникальную автоматическую линию по изготовлению европоддонов. Ее обслуживает всего два оператора, она способна выпускать больше 2 000 поддонов в сутки. Аналогов в России с такими параметрами точно нет. Возможно, в перспективе мы не только будем делать такие линии, но построим целый завод по производству этой востребованной продукции где-нибудь на Урале.
Самое важное - в нашем Telegram-канале