Рязанская «дочка»
В холдинг «Русская кожа», чье головное предприятие располагается в Рязани, входит несколько крупных заводов. Один из них находится на юго-востоке Испании, а другой - в Алтайском крае.
Идея построить завод по переработке шкур крупного рогатого скота именно в Заринске не случайна, рассказывает генеральный директор Ольга Усова.
Ольга Усова,
генеральный директор Заринского кожевенного завода:
В Сибирском федеральном округе сосредоточено 25% необходимого сырья. Этот факт уже во многом объясняет нашу локализацию.
Что касается Алтайского края, это сельскохозяйственный регион, полный крупного рогатого скота. Наша миссия – переработка шкур животных, как побочного продукта мясной и молочной отрасли, в ценный материал. Сохранение природных ресурсов - часть нашей модели бизнеса.
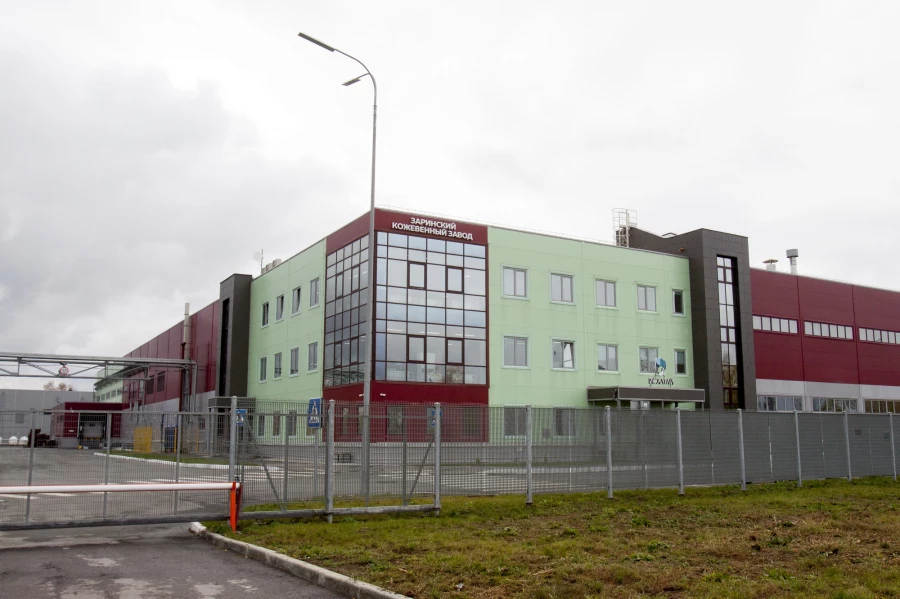
Директор встречает нас в своем офисе. Тут несколько диванов благородного изумрудного оттенка и мягкие кресла. Все из кожи собственного производства. Вдоль стен расположены стеллажи с подсветкой, в которых рядами вывешены выставочные образцы.
Одни представляют собой готовый материал для обуви, другие — для одежды, третьи — для мебели. Их отличие можно легко определить на ощупь. Например, мебельная кожа более мягкая, ременная – жестче и толще. Впрочем, о характеристиках сырья мы расскажем еще много.
А пока вернемся к истории самого молодого кожевенного предприятия в России. Отстраивать его начали в 2017 году. Вложения были немалые — 2,1 млрд рублей, включая импортное оборудование.
В 2019 году завод «Русская кожа — Алтай» начал работу.
90% шкур на предприятие доставляют напрямую с убойных пунктов и мясокомбинатов Алтайского края и других регионов Сибирского федерального округа. 10% приходится на Казахстан и Монголию.
Пороки и идеалы
Поиск поставщиков, подчеркивает Усова, начался задолго до открытия. За три года после начала работы завод перешел на прямое сотрудничество с убойными пунктами и мясокомбинатами.
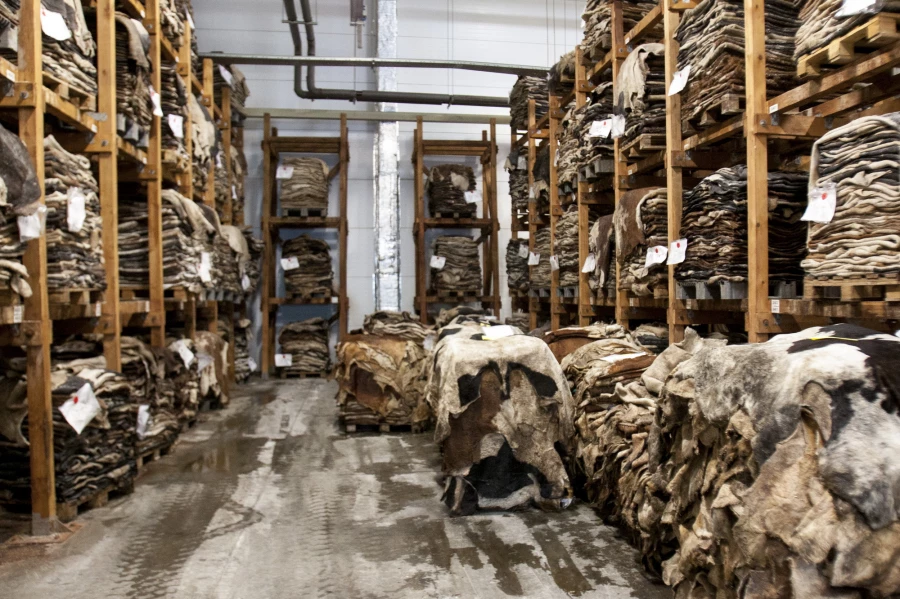
«Работа без посредников выгодна как нам, так и самим поставщикам — они знают, куда могут направить шкуру. А мы уверены в ее качестве, - рассказывает Ольга Усова. - Общение через третьих лиц позволяет настроить обратную связь на должном уровне».
В мире кожевенного производства слова «качество» и «порок» неотделимы. Чем меньше «пороков» - врожденных или приобретенных недостатков на шкуре, тем выше ее качество. Многое зависит от условий, в которых содержали животных.
Эксперт объясняет: «Если за коровой плохо ухаживали, на коже останутся царапины, укусы насекомых. Или она могла сама на выпасе зацепиться за ветку дерева — останется шрам. Всего и не предугадаешь. Зачастую фермеры не уделяют этим процессам должного внимания: допускают прорези, дыры и даже гниение шкур. Поэтому идеальный, без изъянов, материал встречается нечасто».
Однако даже сырье с большим количеством дефектов, не идет на выброс.
«Мы ничего не утилизируем. Разложение шкур принесет огромный вред экологии, - говорит Ольга Усова. - Мы разработали технологию переработки материалов низкого качества в белковые продукты. Они годятся для изготовления кормов, производства желатина, колбасных оболочек. А также спортивных добавок. Ведь кожа — это чистый коллаген. Его употребляют, например, культуристы».
Факт
Не более 10% белковых побочных продуктов из общего объема сырья получает Заринский кожевенный завод ежемесячно.
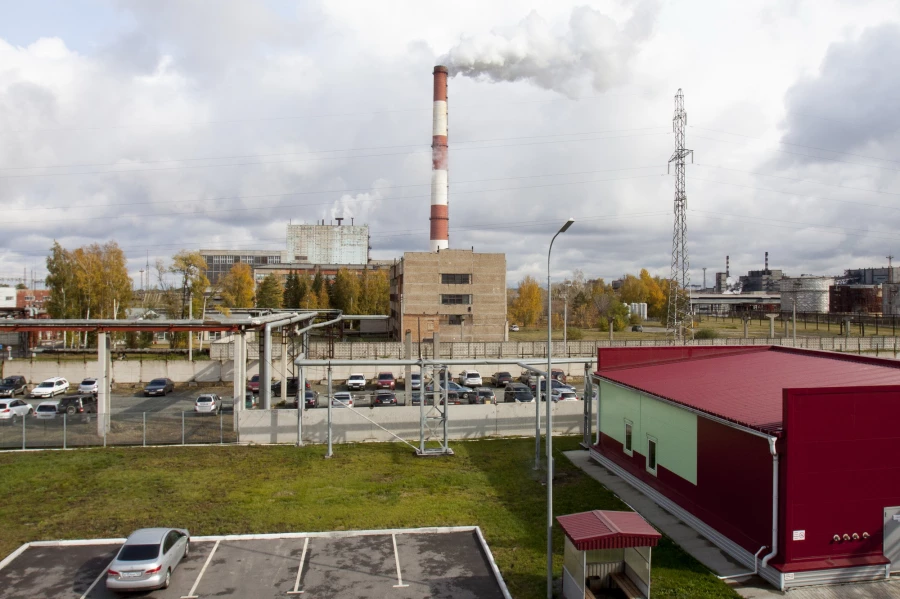
От консерванта — до кожи
С первых минут после съема начинается процесс бактериального разложения шкуры. Поэтому ответственность поставщика — правильно, не жалея соли, законсервировать продукт.
Сырье хранится в отдельном большом помещении. Фактически это - склад-холодильник. Здесь пачками разложен необработанный материал. В таких условиях он может храниться долго. Зрелище и запах не для впечатлительных или вегетарианцев.
Первый этап обработки — обессоливание. Агрегат для этого находится прямо в цехе и похож на овальную решетку. В нее загружают сырье, получая на выходе чистую шкуру.
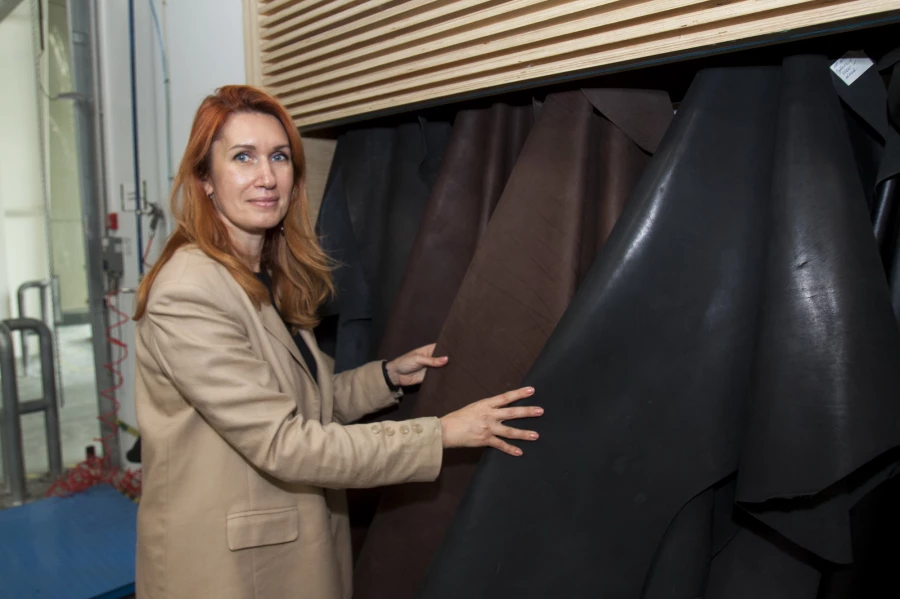
На такую красоту ставят клеймо и отправляют на взвешивание и сортировку. Последнее — вручную и с помощью специальных гаджетов, чтобы не пропустить ни одного порока.
По словам Ольги Усовой, ежедневно на предприятии обрабатывают до 20 тонн материала.
Следующий шаг — операция отмокозоления. Она могла бы называться, как популярная в начале 2000-х телепередача «Большая стирка». Все потому, что шкуры отправляются в гигантские пластиковые барабаны, точь-в-точь стиральные машины. В одну вмещается семь тонн сырья.
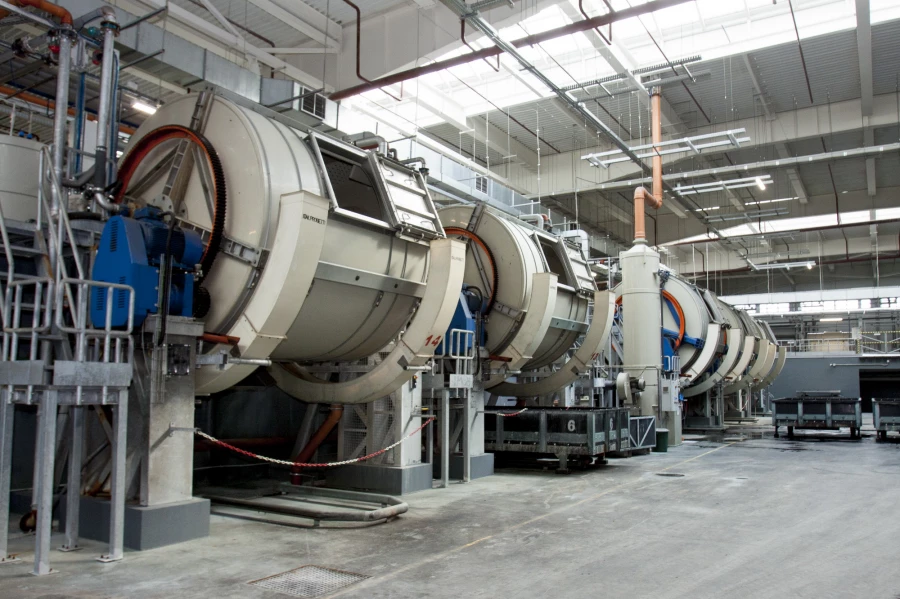
С этого этапа и далее работникам остается только управлять процессами с помощью специальных пультов в диспетчерской. С этим справляются один-два сотрудника.
Стиральных установок в помещении несколько. Каждая может работать в разных режимах. В качестве «порошка» используют смесь химикатов. Для этого используются российские компоненты. А пока мы наблюдаем, как очередная партия отправляется «стираться», расскажем про оборудование.
Основные производственные процессы автоматизированы. Подача, дозирование и смешение химических материалов происходят бесконтактным способом.
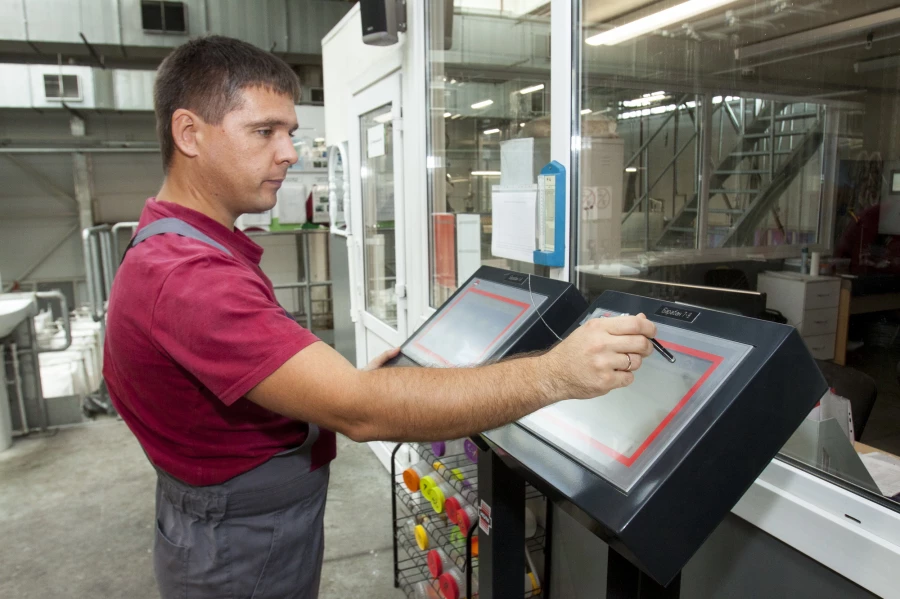
Вся техника на Заринском кожевенном заводе импортная. 90% - из Италии, 10% - из Германии и Швейцарии. Всего более 80 позиций. Запчасти, рассказывает Усова, меняют регулярно, чтобы машины могли работать круглосуточно и бесперебойно. Проблем с деталями пока нет — имеется запас.
«Облачный» полуфабрикат
Через двое суток стирки шкуры превращаются в голье – сырье без волосяного покрова.
Третий этап — дубление. В этом цехе в таких же барабанах шкуры не мокнут, а проходят обработку уже с другими химикатами. Так голье превращается в полуфабрикат.
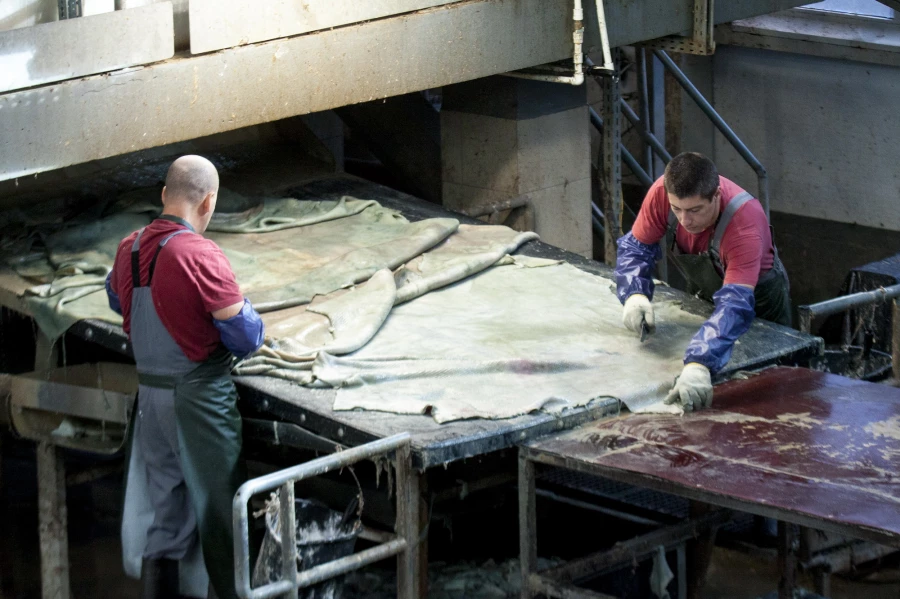
«Таким образом, волокна коллагена химически связываются, структурируются, - рассказывает Ольга Усова. - После этого будущая кожа не поддается гниению, а также способна выдерживать высокие температуры».
В таком виде материал выглядит как светлая джинсовая ткань или облачко. На ощупь полуфабрикат очень мягкий, близкий к готовой коже. Название соответствующее — wet blue – «влажный голубой». Кстати, влажность должна быть строго определенного уровня, иначе изделие может испортиться.
Затем пласты разрезает двоильно-ленточный аппарат. «Облачка» толщиной не более 1 мм встречают работники и отправляют в красильно-жировальные барабаны.
Из названия понятно, что тут материал, наконец, приобретает ровный цвет. Можно сделать любой: хоть фиолетово-розовый. Но самые популярные у заказчиков - черный, бежевый и коричневый.
Дальше почти готовый продукт ждет сушка. Это тоже не быстрый процесс, ведь кожа должна быть эластичной. В целом, все этапы обработки сырья от шкуры до краста (так называют полностью обработанную шкуру) занимают примерно 15 дней.
Экологический вопрос
На предприятии имеются очистные сооружения. Стоки из каждого цеха очищают. Директор рассказывает, что такие системы сегодня применяются лишь на 2% кожевенных предприятий в мире. Они позволяют многократно использовать отработанные стоки, сократить расход химикатов и воды.
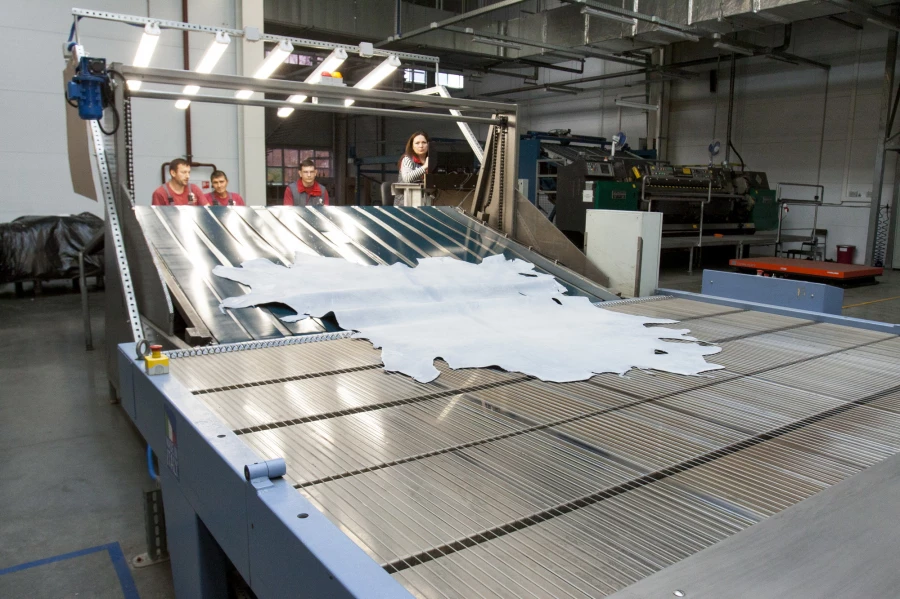
Куда едет кожа
Основные каналы сбыта алтайской кожи — страны Азии. На них приходится 70% товара. Остальные 30% - внутренний рынок. Кроме того, предприятие планирует наладить сотрудничество с Индией и Пакистаном.
Из заринского материала шьют одежду, обувь, аксессуары. Кстати, шикарные сапожки «из кожи крокодила» сделаны совсем не из нее. Скорее всего, это хорошо обработанная кожа коровы или быка.
Факт
В заринскую кожу «наряжены» салоны автомобилей Renault, Nissan, Aurus, самолеты авиакомпаний S7 и «Аэрофлот».
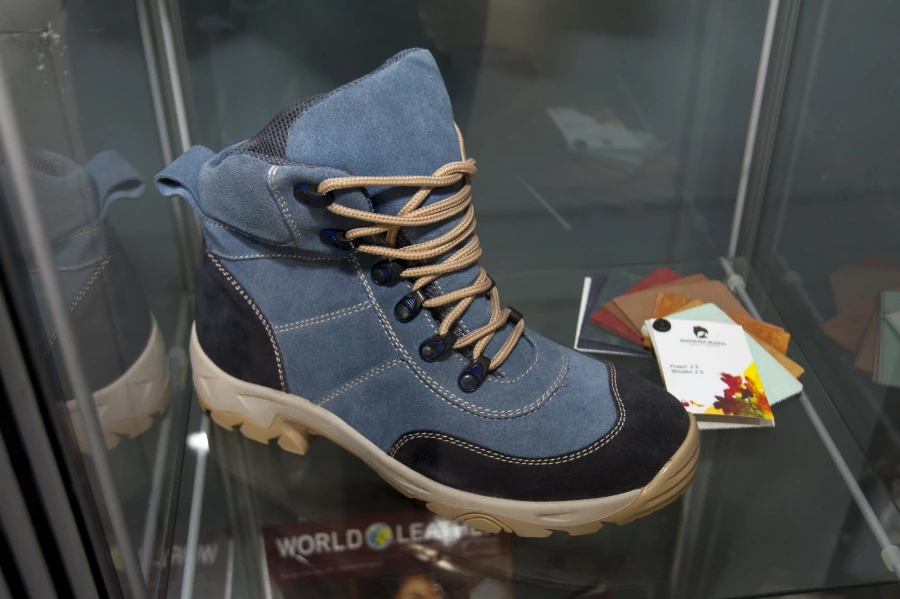
Кадры и мобилизация
Сегодня на предприятии трудятся 144 человека. График работы зависит от должности. Некоторые предполагают как дневные, так и ночные смены. Средний уровень зарплаты, уточняет генеральный директор, 47 тыс. рублей. На старте можно рассчитывать на сумму от 33 тыс.
Вопрос кадров в случае с заводом «Русская кожа — Алтай» решился еще на этапе его строительства. Часть сотрудников обучили специалисты головного предприятия в Рязани. Передавала опыт и сама Ольга Усова. Она стала генеральным директором Заринского кожевенного завода в 2022 году, сменив Сергея Филатова. До этого руководила запуском и производством.
В свете последних событий мы не могли не спросить про то, коснулась ли завода частичная мобилизация. Ведь большинство служащих мужчины — их в штате 88.
На момент подготовки материала призвали только одного человека. Еще двое — решили пойти добровольцами. Усова надеется, что частичная мобилизация не отразится на работе предприятия.
Цифры
- 600 тонн сырья предприятие может перерабатывать ежемесячно.
- 100 постоянных поставщиков у Заринского кожевенного завода. 35 из них — в Алтайском крае.
- 60% шкур на Заринском кожевенном заводе — от коров, 40% - от быков
- До 100 тыс. кв. м готовой кожи в месяц способен изготовить завод.
Самое важное - в нашем Telegram-канале